The solution for paper mill waste – CBI team at the final of the ChemPLANT competition in Berlin
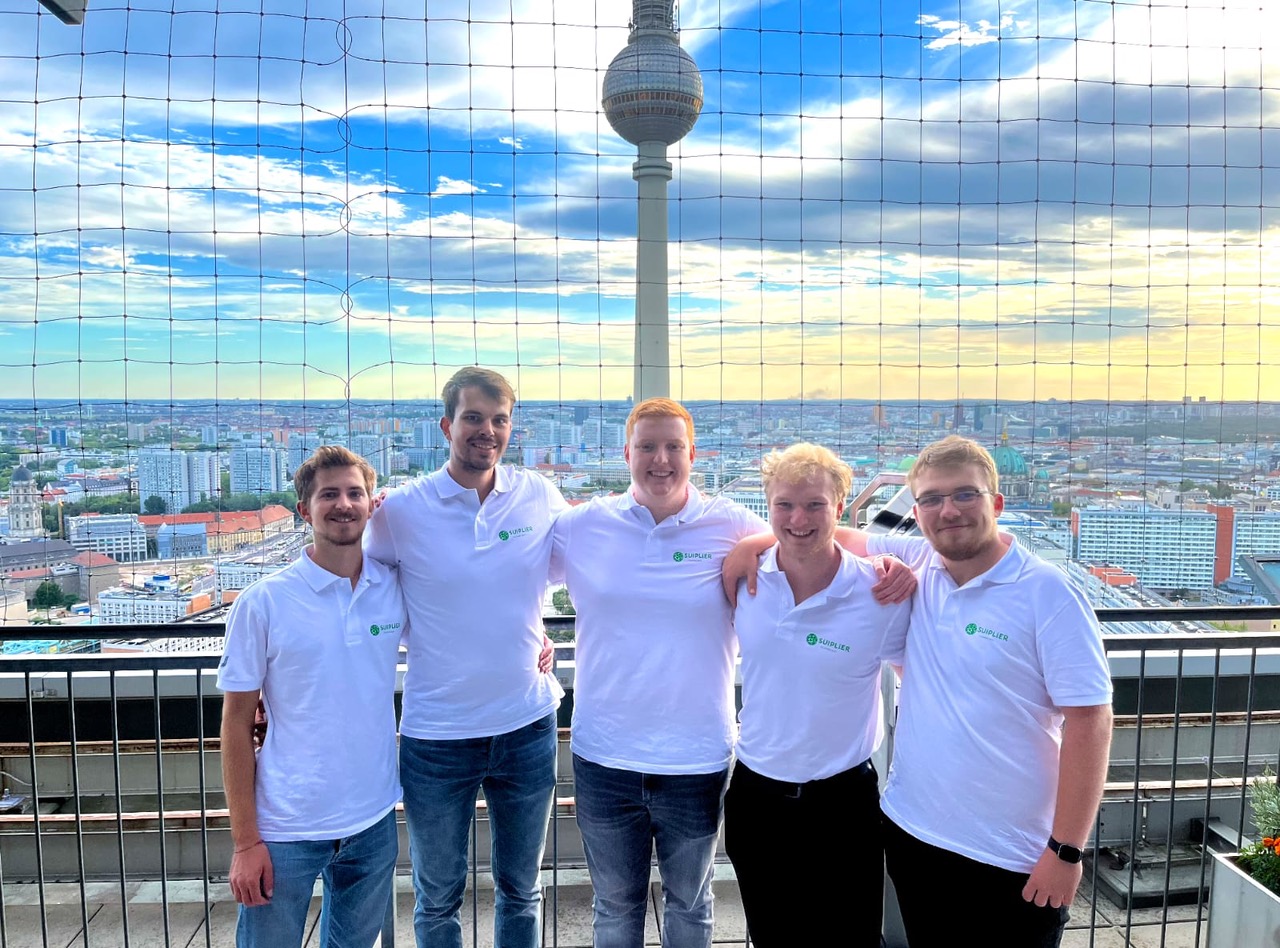
Everyone knows it, everyone uses it and everyone knows it somehow comes from trees. Paper!. How are papers made? They’re made in a paper mill. But how exactly such a factory works, that’s where it stops for most people. At the beginning of the year, a few students from the CBI Department asked themselves what exactly happens to the wood that ends up in the paper and what happens to the rest?
But it wasn’t just a matter of expanding their knowledge to show off. The question came from this year’s ChemPLANT competition. Every year since 2018, the KjVi – the “creative young process engineers” of the VDI (Association of German Engineers) organize a Germany-wide competition in which students from universities can compete in the field of process engineering. The aim is to solve a process engineering problem as creatively, innovatively, but realistically as possible and to develop a meaningful concept.
Five young engineers from FAU have taken up the challenge and considered how the wastewater stream from a paper mill, called black liquor, can be used in a way other than just thermally as before.
The answer is: “SUIPLiER – we provide Lignin”. The “Sustainably Usable Inter-Processual Lignin Erlangen”.
The five-member team, consisting of group leader Nils Dünninger as well as Julian Grüber, Gabriel Mark, Jörn Klose and Nils Montag are responsible for this name. Their innovative concept is as follows. With the help of nanofiltration, the lignin that remains from the wood during paper production is separated and purified for sale. Another partial stream, consisting of water, organic acids and sugars, is converted into saleable biogas in a biogas plant. The remaining inorganics are separated from sediments and returned to the paper mill as recycled material together with residual water. In addition to the sales products, the key points were above all the energy self-sufficiency of the process and a reduction in the CO2 footprint. It was also important to the developers that the concept could be used as efficiently as possible at existing sites without having to install large-scale chemical plants.
With this concept, the young engineers were able to beat several other German universities and made it to the finals in Berlin. This is a remarkable achievement that was last achieved by a team from FAU in 2019. This time, however, there was an additional, more site-specific hurdle. The latter three participants were on ERASMUS+ semester abroad (all in Athens, Greece) at the same time of the competition. Due to the distance, the entire concept was split between two countries and was put together by MS teams. At the end of July, a finished concept report with all technical details, used equipment, a cost analysis and CO2 and energy balance had to be handed in. A whole project planning, which must hold costs up to the last employee of the factory.
The work was worthwhile in the end, because the final participation also included an entrance ticket to the “14th European Congress of Chemical Engineering” (ECCE), which took place at the same time as the “7th European Congress of Applied Biotechnology” (ECAB) from 17.-21.09.23. The finalists went together to the “14th European Congress of Chemical Engineering” (ECCE).
So it went for the finalists together with seven other university representatives to the capital. On Monday, the teams had to prove themselves in front of a jury consisting of representatives of companies such as BASF and Bayer as well as professors and had to present their concept convincingly.
The subsequent poster presentation was a general exchange between the teams and the other participants of the conference, where also other PhD students and professors of the Department CBI participated and presented their work.
Unfortunately, it was not enough for a podium place for the SUIPLiER “founders”. According to the jurors, all participants were very strong, but in the end the team from RWTH Aachen was able to prevail with its concept. However, the basic idea of the Aachen team is not dissimilar to that of the FAU, so the representatives from Erlangen were on the right track. However, the motto “To be there is everything” is also fully valid in this final. The experience of conceptual design, participation in the European conference, an organized pub quiz, and a city tour of Germany’s capital were definitely worth the work. The participants are proud to have represented FAU in this way and can be justifiably satisfied with their performance.
The next version of the ChemPLANT competition will hopefully take place again next year with a strong team from FAU. The participants would like to express their sincere thanks to Prof. Marco Haumann (CRT), Dr. Nicola Taccardi (CRT), Dr. Holger Hübner (BVT) and Dr. Detlef Freitag (Head of High Pressure Laboratory) for their support in the preparation. Also, a big thank you to the members of the KjVi for organizing the competition and the umbrella organization VDI.
Written by Nils Montag